Automation Leads The Way In Food Safety Inspection Systems
By Melissa Lind, contributing writer
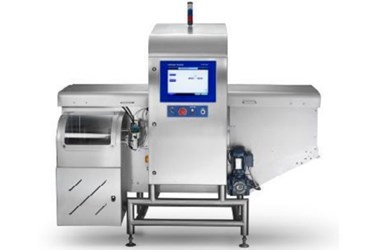
The Food Safety Modernization Act will require food producers to shift focus from reaction to prevention. It will also place primary responsibility for food safety concerns on industry members, while expanding the FDA’s authority in terms of recalls and production suspensions. With such widespread changes approaching, automation might help ease the transition.
Since the 1960s, the food industry has viewed Hazard Analysis and Critical Control Points (HACCP) as the backbone of food safety assurance. However, in 2013, the Proposed Rule for Preventive Controls for Human Food may require additional actions. The FDA is taking a broad approach in a revised position that acknowledges that science and risk-based metrics are needed, while allowing that flexibility in implementation is also essential.
Preventative measures ensure that hazards that are “reasonably likely” can be minimized and are requiring industry partners to stretch beyond the traditional HACCP view when establishing policies and procedures to meet the new FSMA requirements. Each company should create a thorough, written plan which identifies potential hazards and operational controls with maintenance plans. Ideally, the safety plan will be managed by a team, rather than an individual, and will identify how controls will be validated and verified with maintenance on a routine basis.
Inspection systems are a vital part of FSMA implementation and automation is the way to go. Automated systems that can easily record data which will comply with regulatory requirements as written or electronic documentation are critical. The most common automated, food-safety inspection systems include:
- Weight-measurement systems that ensure that packaged products are accurately filled and correspond with labeling. Modern systems operate seamlessly with the processing line without slowing production
- Metal-detection units ensure that products are free from metal contaminants which can enter in raw ingredients or during processing. Many metal-detection systems are flexible in placement to enable identification at various points in the processing line with automatic rejection for failed units
- Video monitoring uses camera and software combinations to inspect products or packages for defects. A captured image is compared to a reference image for automated rejection. These systems can detect malformed products, incorrect volume, labeling defects, inadequate seals, and improper placement.
- X-Ray detection systems are highly flexible and are often used for multiple tasks. X-Ray systems can detect a wide variety of high-density contaminants and can also identify incorrect count, defective product, improper placement, missing components, and closure defects. X-Ray systems can be used at many points in the processing line and are effective with more than one product type being processed simultaneously.
Many newer inspection systems can increase efficiency and operate with fewer man-hours by automating rejection process and data collection processes without slowing the production line. This enables manufacturers to reassign workers to other vital areas. Initial capital expenditure may seem high, but it can pay off big in terms of increased efficiency, reduced threat of necessary recalls, and increases in consumer confidence and brand loyalty.