Clean, Safe Conveying – The New Wide Belt Solution
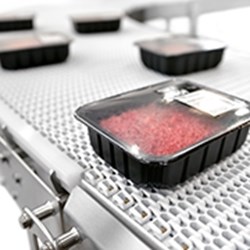
At Interpack, FlexLink unveils its latest innovation for safe, clean and efficient handling in primary and secondary packaging for the food industries.
Sustainable packaging concepts are important contributors in the reduction of losses in the food production and supply chain. The latest development from FlexLink, the new wide belt conveyor, addresses some of the higher hygienic requirements associated with primary and secondary packaging.
Hygiene and safety are priorities
For operators, the cleaning process is fast and easy and the new wide belt stainless steel conveyor, WLX, sets new standards for cleaning results and cleaning process time.
“We are extremely proud of this design, because we’ve succeeded in optimizing both product safety and hygiene to a very high level, following the industry requirements and regulations. For instance, flat surfaces have been eliminated and there are no hollow bodies or crevices where bacteria will grow“, comments Tommy Karlsson, Innovation Manager at FlexLink.
The new conveyor is safe, silent and ergonomic and it is easy for operators to lift the chain for cleaning. Operator safety has been served for by a thorough design work resulting in minimal openings to prevent pinch points, and absence of sharp points and edges. Finally, the noise level is comfortably low to the benefit of the factory environment.
Reduce the cost of ownership
With the innovative design and the refined standardization, factories will benefit from good hygiene and a trouble-free operation. The total cost of ownership is considerably reduced by features of the new design and sophisticated solutions.
A good example is the quick and efficient cleaning process which saves substantial amount cleaning time and releasing more time for production. The easy lifting of the chain and good access to the interior with clean surfaces makes a difference and the cleaning time can be reduced by as much as half.
The lead time from design to installation is very short thanks to the standardized and modular design combined with FlexLink‘s global distribution network and short delivery time. Once installed, downtime is minimal due to the robust design, and there is minimal power, water and detergent consumption. All this helps lowering the total cost of ownership.
Versatile
The WLX wide modular plastic belt conveyor is available as components, modules or a complete system. The system is available in three widths and is well suited for the handling of pouches, standing pouches, liquid carton packaging, cases, bundles, trays or smaller products in mass flow. The belt easy to clean and available in 304 mm (12 inch), 456 mm (18 inch) and 608 mm (24 inch) widths.
“Feedback from the industry is genuine and customers are very pleased with our new wide belt conveyor system in stainless steel. We have reached a fully modular design that not only supports operators in more easily performing their daily tasks, but also increases available production time. Furthermore, as the WLX is a standardized conveyor platform, you always know what you‘ll get and how to maintain it. In the next development we will meet requirements on hygienic design for direct food contact“, concludes Tommy Karlsson.
Source: FlexLink