Food Safety Initiatives Are Pushing Hard For Food Testing Lab Accreditation
By Laurel Maloy, contributing writer, Food Online
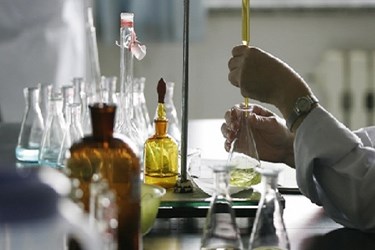
The number of food processing plants closing their in-house food plant labs and outsourcing to corporate or independent food contract labs is on the rise
Until about 30 years ago, almost 100 percent of food processing facilities had their own laboratories for food safety testing. Food samples were collected from the raw materials, from the production line, and from the final product for laboratory analysis.
Today’s testing standards are more complex, testing equipment is more expensive, and the ongoing training necessary to staff a food plant lab (FPL) continues to increase. As the requirements for documentation increase and regulations become more stringent, companies have been forced to reevaluate the cost vs the value of maintaining an FPL. Additionally, due to increased cost and complexity, some food processing companies have restricted the types of tests that can be run in-house. Pathogenic testing has become so cost-prohibitive and complicated, that many food companies have found outsourcing these tests to be a more economically sound and more widely accepted practice.
Vision Inspection: Now Vital For Food Safety
Strategic Consulting (SCI) estimates that out of the approximately 40,000 food processing plants worldwide with 25 or more employees, just 86 percent maintain and utilize an FPL today. As a result of the growing number of widespread food adulteration cases, many resulting in severe illness and death, the focus on food safety is sharper than ever. The Food Safety Modernization Act (FSMA) was signed into law in 2011, putting the issue of food safety on the fast track for improvement. Since that time, alliances such as the Global Food Safety Initiative (GFSI) and the Food Laboratory Alliance have emerged, advocating for the consumer and global food safety. These initiatives are pushing hard for third-party accreditation of food testing laboratories. Meanwhile the FDA and the USDA continue to sort through the rules on lab accreditation.
Additionally, the accreditation process itself is costly. Most FPLs will be required to put new, state-of-the-art systems in place, as well as training existing staff or hiring additional personnel to run the labs. The accreditation review fee alone can run more than $15,000 and continued compliance means continued costs. It is also true that a lack of trust from food company customers raises the question of the viability and reliability of in-house lab results. Results from a third-party lab are preferred in most cases.
SCI has drafted the first-ever report examining the growth of the food contract lab (FCL) market. The report clearly indicates that the FCL market is growing faster than the food safety testing market and that FCLs are taking the market share. Some FCLs will provide an on-site, semi-mobile lab, or will even utilize the existing FPL space at a food processing facility. Their competitive pricing structure includes testing for pathogens, nutritional analysis, and chemistry testing for pesticides, toxins, and other contaminants. In some cases, the FCL is a one-stop-shop for food safety testing, food safety program development, field and plant assessments, and third-party process audits.
SCI’s report concludes that the push for food safety lab accreditation may be the “tipping point” for food processors, forcing them to turn to independent FCLs in order to comply. Some processors may be fighting the changes tooth and nail, but the savvy are definitely realizing that this may not be such a bad thing after all.