Hormel Foods' Sustainability Goals — Less Space Mean Less Waste
By Karla Paris
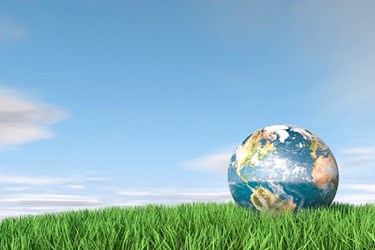
Releases on May 15, the company’s the eighth corporate responsibility report discusses all aspects of the company’s initiatives related to the environment, animal care, its products, its people, and the global community.
Packaging is a vital component of Hormel’s corporate responsibility goals. The company assigns a group of employees who continuously look for minimization opportunities, while participating in a corporate initiative to reduce materials in packaging.
In 2013, each member of the team was tasked with identifying 500,000 pounds of materials that could be reduced and translated into savings. This amounted to a group goal to reduce packaging by 4 million pounds each year. The packaging team works with all departments and examines the entire supply chain for initiatives related to sustainability that will benefit all divisions. In 2013, this team initiated more than 60 total projects and completed 37 of them. Combined, these projects resulted in a package reduction of 4.72 million pounds per year.
In 2013 alone, Hormel Foods’ packaging redesign efforts yielded a reduction in packaging by nearly 5 million pounds, which is almost 20 percent of the company’s long-term goal to reduce product packaging by 25 million pounds. Examples where Hormel Foods and its corporate packaging initiative found savings include:
- Eliminating excess space inside the brown carton of Hormel Natural Choice deli meat packaging. By reducing the packaging from roughly 8 inches wide to 6.55 inches wide, Hormel was able to reduce the amount of paperboard, film, zipper and corrugated material used, resulting in a savings of roughly 800,000 pounds of packaging material.
- Optimizing the shipping case design for its retail 1 lb. bacon by changing from a full overlap case to a 1-inch overlap case. This resulted in a savings of more than 364,000 pounds.
- Introducing a machine set up caser and palletizer for its cooked hams line. The company’s cases were redesigned to run on the automated line, which resulted in an annual savings of 596,000 pounds.
- Switching to an industry standard tote bin design and eliminating an internal insert amounted to a savings of nearly 1.3 million pounds.
- Removing j-board, a paper carrier board, by moving to a fully printed film for its 1 lb. retail turkey bacon. This resulted in a savings of over 310,000 pounds.