Preparing For Digital Supply-Chain Traceability
By Melissa Lind, contributing writer
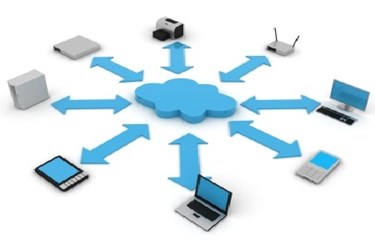
Just like almost every other industry, the food-supply chain is going digital. Some sectors of the food industry have tracking and traceability data collection and management under control, but others do not. Is your company prepared for the inevitability of electronic communication requirements?
While some food processors are currently managing to meet regulations through paper tracking and documentation, this information is not easily usable by the next user down the line. As the amount of data worked with continues to expand, movement to electronic records must occur and your company needs to make sure its system can communicate with both suppliers and customers. There are a number of factors that affect how easy it is to provide complete traceability with full visibility for any one particular sector of the food-supply chain including:
Length Of Supply Chain
More steps in the supply chain make traceability a more-difficult issue. This is complicated even further by global expansion, with sourcing of raw ingredients done in far-reaching locales. Many underdeveloped regions do not have well-established tracking and traceability methods and more advance members of the food-supply chain are slowly stepping up to help.
Data Visibility From One Point To Another
It isn’t enough for you to know which materials came from which plant. It isn’t even enough to know which plant has traceability within its own system. Your company needs to ensure it has access to upstream data from at least two suppliers away — and, ideally, can trace a particular food product all the way back to harvest. In addition, your company must be able to provide that data to downstream partners.
Processing Complexity
The more complex a food-processing system is, the more difficult tracking and tracing visibility will be. It is much easier to track a corn product from farm through a single-product grinding facility than it is to track a variety of ingredients through a facility that makes a mixed product for use in baking. In some sectors of the food industry, foodborne illnesses have necessitated government intervention, but other sectors remain behind and contamination can happen at nearly any step in the food-supply chain.
Integration
Integration is likely the biggest issue from a whole-process perspective. Even if each individual processor is up to standards within the facility, ensuring total visibility requires that different systems be able to communicate with one another.
Some sectors have solved the communication issues by establishment of a large data depository where each participant reports in to the same database. One example of this is the Canadian Cattle Identification Agency (CCIA) and Agri-Traçabilité Québec (ATQ) which have brought information from different regions and different types of processing facilities. Once an animal is identified with a serial number, the same animal can be traced through each facility until processing.
Establishing a large database that encompasses every food type is impractical, but the IFT Global Traceability Center has called for the establishment of an industry protocol which would identify a standard format for information storage. Software manufacturers would need to ensure that information is available in the same format for every food type. This format requirement would be similar to the way that GS1 barcode formatting is done. Rather than requiring that each processor report in to the same system, information would be available in an easily transferred format upon query.
Some participants in the food industry are still using paper and electronic recordkeeping and tracing solutions. A switch to only digital tracing and recordkeeping has not yet been mandated, but it can’t be far. Getting your facility ready now will help make the transition to data standards when the IFT protocol is complete and similar regulations come into play.