Seven Keys To A Bona Fide Food Recall Plan
By Laurel Maloy, contributing writer, Food Online
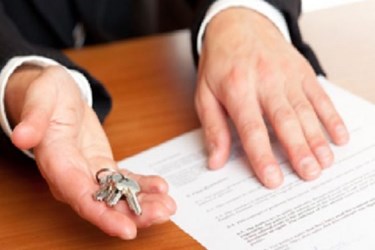
FSMA requires food processing facilities to have a written recall plan in place. Have you drafted yours?
The Food Safety Modernization Act’s (FSMA) Proposed Rule for Preventive Controls for Human Food requires every “covered” facility to prepare and implement a written food safety plan. Included in this is a recall plan. “Covered” is defined as those facilities required to register with the FDA under Section 415 of the Food, Drug, and Cosmetic (FD&C) Act. Voluntary recall procedures are also covered in the USDA’s Food Safety and Inspection Service (FSIS) Directive 8080.1, the most recent revision dated Sept 9, 2013.
FSMA does away with the one-size-fits-all approach to food safety. It sets forth new provisions on hazard analysis and risk-based preventive controls and revises the Current Good Manufacturing Practices (cGMP) found in 21 Code of Federal Regulations (21 CFR), part 110 — the new, finalized provisions, revisions, and requirements will eventually be found in 21 CFR, part 117.
Even if it were not mandated, it makes good business sense to have a written recall plan. The most obvious reason is that in the event of the absence of the responsible person, the recall can be handled quickly, efficiently, and above all, correctly. A written checklist will ensure that every step has been covered, protecting a company from inadvertently skipping an action that could possibly lead to charges of negligence. FSMA also allows for each establishment to assess its risks and to tailor its recall plan to cover what could reasonably occur within any given facility. Additionally, FSMA, Section 206, gives the FDA Mandatory Recall Authority in the event a covered establishment neglects its responsibility or refuses to implement a voluntary recall.
Having trouble complying with new food safety requirements? Check out these tips.
FSMA, at this point in time, does not dictate what should be included in a written recall plan; it only mandates that one be in place. Here are some suggestions for what a comprehensive recall plan should include:
- Identify the first contact: A food company’s policy should identify the first person to contact in the event a recall is necessary. This person should have the authority to make the decision to implement a recall and to deal with or delegate someone to deal with regulatory authorities and the media. This may be the same person as the recall coordinator.
- Identify a recall coordinator: Food and beverage companies also need to identify the next person in line and at least one other. The people should provide the best possible contact information including: landlines, mobile, short message service (SMS), and email communication. If there is a team in place, one person should be designated to coordinate. This person should be responsible for completely understanding the requirements under Title 9 and 21 of the CFR, FSMA, and Hazard Analysis and Critical Control Points (HACCP). This person may or may not have the authority to make critical decisions instantly, investigate the complaint, contact customers, notify legal counsel, coordinate with vendors and distributors, and communicate with media outlets. Responsibilities of the recall coordinator should be specific.
- Identify Regulatory Points of Contact: Depending upon the type of recall, this may include FSIS, the USDA, and/or the Centers for Disease Control and Prevention (CDC). It may also include the Canadian Food Inspection Agency (CFIA) or regulatory agencies in other countries. Companies subject to a recall are responsible to know who must be contacted and when to contact them.
- Outline the recall process: Spell this out in the order it is to be accomplished. Different recall processes may be necessary for dissimilar situations, i.e.: for processed foods vs. raw, or for exported foods, as opposed to those for domestic distribution. A recall process may differ depending upon where the recall is identified in the manufacturing process. Prioritize and standardize recall procedures.
- Draft a standard recall notification letter: Leave blanks for the reason for the recall, dates of manufacture, the lot numbers, the UPC codes, etc. Be sure to look at FDA recall notices to determine what should be included. As points of contact change, ensure these are updated on the template for the recall notification.
- Verify Recordkeeping: Lot coding, batch numbers, dates, and exact product names are critical for tracing adulterated product and for public notification. Evaluate your recordkeeping processes and make improvements as necessary. Be sure the Information Technology (IT) Department authorizes permissions for computer access to those involved in the recall process.
- Periodically review the recall process: It is critical to ensure points of contact and written recall protocols are kept up to date as personnel and regulatory requirements change. At a minimum, review them annually, anytime there is reorganization within the company, and as key personnel change.
Recalls are unexpected and must be handled within the confines of the law and with due diligence. Having a written plan in place ensures a more organized recall experience at a time when effective implementation is critical.