Smithfield Foods Earns A Whopping 74 Awards For Workplace Safety Innovation
By Karla Paris
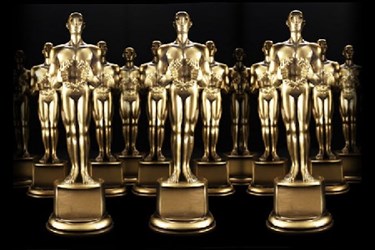
Meatpacking processor uses an employee-driven approach to change behaviors and improve workplace safety
Historically, the meatpacking and processing industry has ranked among the most hazardous professions in the U.S. Food manufacturing workers are twice as likely to experience injuries and illnesses than industrial and manufacturing workers as a whole. The meatpacking industry also ranks high for severe injury and illness cases — meaning those that cause workers to miss days at work, or those necessitating restricted work activities or even job transfers. Ensuring its employees’ safety is a top priority for any manufacturer, especially one in this market.
Smithfield Foods announced on April 30 that the company's facilities across the United States received a total of 74 awards this year from the American Meat Institute (AMI) Foundation for outstanding achievements in workplace safety. Additionally, the company received 35 Environmental Recognition Awards. Much of Smithfield Foods’ success in advancing its workplace safety stems from advances made to its Employee Injury Prevention Management System (EIPMS,) audit process, and conducting further EIPMS and auditor-certification trainings.
In fiscal 2013, Smithfield Foods rolled out its behavioral risk improvement (BRI) process at several new facilities, and then scaled the program throughout its other U.S. facilities. The company’s BRI process is comprised of a four-step safety program:
- Visible and measurable engagement at every level of management
- Exceeding all regulatory requirements
- Managing safety as a process
- Addressing human behavior
One of the key aspects of BRI is that it is an employee-driven program. Within it, management does little more than support employees in safety efforts. After a comprehensive evaluation that requires several days of on-site observation of line employees and management, each site undergoes an intensive training program involving between 20 and 30 percent of employees at a plant for two workdays. Once the training is complete, each facility is divided into work groups that develop specific safe behaviors that are measured on a daily basis. The program teaches employees how to observe their peers, along with how to give and receive positive and constructive feedback. Examples of safe behaviors range from making sure one doesn’t encroach on someone else’s workspace to using a horn when driving a forklift through a plant’s intersections.
The BRI program has led to huge improvements in safety performance at various facilities. According to the U.S. Department of Labor’s Bureau of Labor Statistics, beef and pork processors report 6.9 injuries per 100 employees on average — more than twice the average for all private industry occupations. Smithfield’s injury rate is just 4.6, more than 30 percent below the average for beef and pork processors. That rate also moves the company closer to its goal of being under the average for all private industry occupations. With several other facilities slated to fully-integrate the company’s BRI process in fiscal 2014, Smithfield Foods’ safety systems and programs go well beyond regulatory requirements, protecting employees while reducing the company’s workers’ compensation costs.