The Function of Steam Jet Ejectors in Processing Fats and Oils
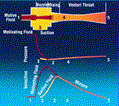
By Henry Hage, vice president, Croll-Reynolds, Co. and Paulo Teixeira, Jr., general manager, Torr Engenharia De Vacuo E Processo Ltda, Brazil
Table of Contents
Keys to Efficient Vacuum System Design
Price Differences
Conclusion
For many years, steam jet ejectors have offered a reliable and economical means of producing vacuum in fats and oils processing. They have a low installed cost and, through the simplicity of their construction, provide years of trouble-free operation. Steam ejectors continue to evolve with the development of new materials of construction, new nozzle configurations and other innovations that enhance the benefits of the basic technology.
The principle of operation of a steam jet ejector is very simple.
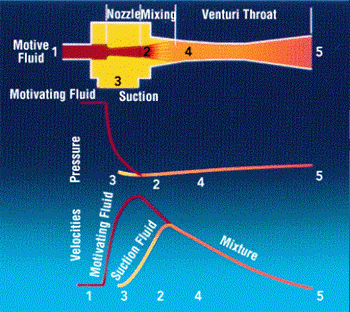
A high pressure motivating fluid enters at 1 and expands through the converging-diverging nozzle to 2, the suction fluid enters at 3 and mixes with the motivating fluid in the mixing chamber 4; both fluids are then recompressed through the diffuser to 5.
Customers in the edible oil industry, like everywhere, are always looking to improve efficiencies and get more from their existing equipment.
Keys to Efficient Vacuum System Design
A vacuum system should not be designed too "tight." This doesn't mean that a huge safety factor should be applied, but only that the tried and true engineering practice be observed.
The following example shows two vacuum systems. System A is designed tight and System B using good engineering practice.
Let's say that our customer is located in a tropical country and that the plant site is approximately 2625-ft (800 m) above sea level. The deodorization unit is designed for 400 tons/day of soybean oil.
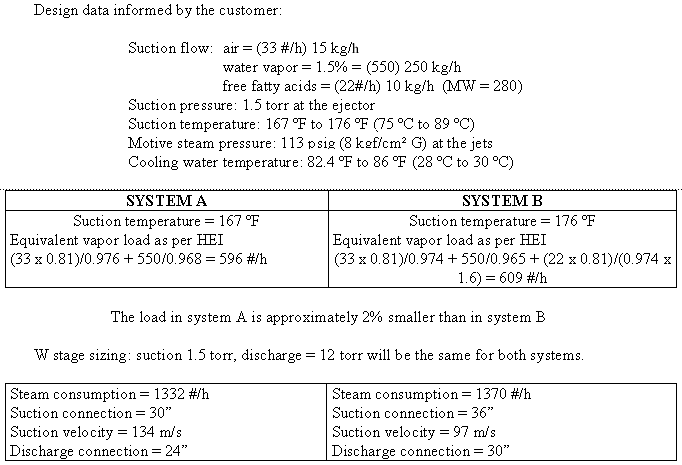
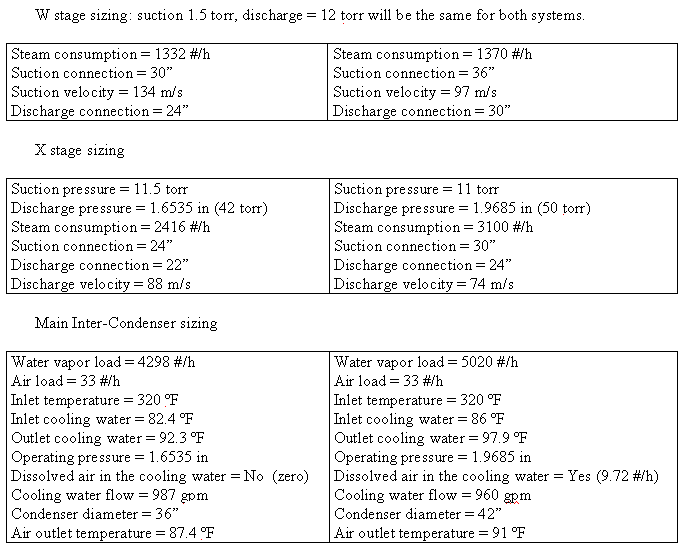
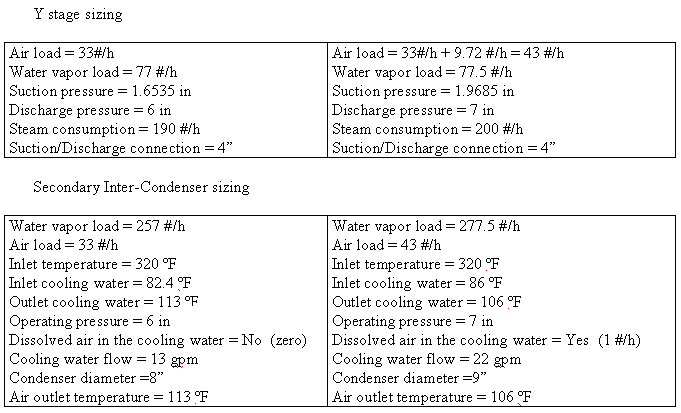
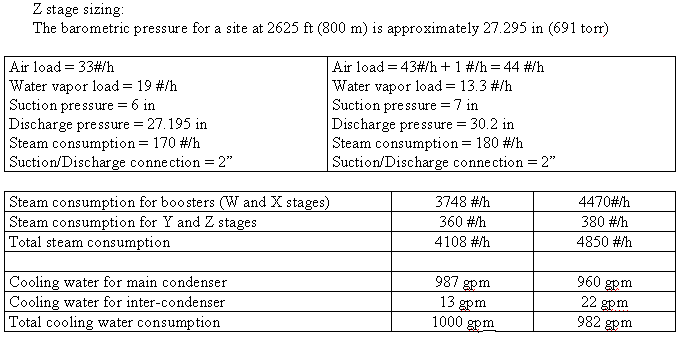
Keep in mind that a vacuum system must be designed for the worst conditions, otherwise it will not work properly if and when those conditions occur.
The differences between the two systems:
- The velocities inside the scrubber lies between 40 to 60 m/s. The suction velocity of the W stage should not be higher than 120 m/s, in order to avoid the conveying of small droplets of oil and fatty material from the scrubber through the jets.
Higher velocities will also generate a high pressure drop in the scrubber, reducing its efficiency.
The oil and fatty acids conveyed into the vacuum system, depending on the layout of the boosters, will rest in the bottom of the head of the jets and sometimes also in the first and second cones of the diffuser, reducing the performance of the system.The oil and fatty acids will also contaminate the cooling water and the cooling tower.
- The discharge pressure of the W stage and the suction of the X stage are, in theory, exactly the same but the performance of the system as a whole depends on the interstage pressures and these two jets are not allowed to fail. In order to prevent failure, an overlap between the two pressures is mandatory.
- The main condenser must be designed for the maximum cooling water temperature, even if this temperature happens only some weeks of the year. A good condenser should be designed to operate at a safe pressure. It is not reasonable to buy a system using a lower steam consumption and having to change the jet nozzles, using more steam in order to try to reach the available condenser pressure.
- The load to the Y stage must also consider the added load of air that is released by the cooling water. This is more critical in the main condenser.
- The velocity at the inlet of the condensers must also be limited to 80 m/s. Higher velocities will also cause problems of pressure drop, poor operation and fast material wear.
- The discharge pressure of the Z stage must always consider a safety factor, because this last stage hardly discharges directly to the atmosphere. It is very common to discharge it into the hotwell.
These are the basic technical points that are rarely checked by the buyers and users of a steam jet vacuum system.
In this example we considered the use of a direct contact condenser. The use of surface condensers is also possible but a little more complicated. The perfect selection of the operating pressure of a surface condenser must take the following into consideration:
- If the vacuum system will use only ejectors, or if the Y and Z stages will be replaced by a liquid ring vacuum pump.
- The highest cooling water available.
- The quality of the cooling water.
- The fouling factor that should be applied to both sides (tubes and shell).
The operation of the vacuum system with surface condenser will be smooth if a recirculation circuit with soda + condensate driven constant to the top bonnet of the condenser is kept at the bottom bonnet with a pH of 10.
Price Differences
Price differences are easy to explain once we understand the technical differences. Well-designed equipment is physically larger than others and as a consequence will cost more.
There is also the "manufacturing quality" factor, which includes the quality of the labor and the quality of the plates, welding material, manufacturing facilities, etc. The mechanical design of the equipment and corrosion allowance will also affect pricing once thicker plates are used.
Another important consideration when comparing prices is the level of technology involved. State of the art equipment will cost more than a cloned one as well as equipment whose performance has been checked in a test bench.
Any time a system is quoted, please use the following list to evaluate the proposal:
The application of your vacuum system and the capacity of the plant (deodorization, bleaching, hydrogenation, extraction, etc).
Suction mass flow for each component, even if in small amounts or traces.
Suction pressure at the suction of the ejector. Always the absolute pressure. Never the pressure inside the equipment.
Suction temperature.
Maximum cooling water temperature, and admissible delta T.
Motive steam pressure at the ejector. Never at the boiler or at the inlet of the building.
Barometric pressure of the plant site.
Where are you going to discharge the last stage.
Conclusion
Steam jet ejectors provide the most reliable and economical means to perform many of the core processes in processing fats and oils. Of all vacuum-producing devices, the steam jet ejector is the most forgiving.
Steam jet ejectors are a reliable and economical means of producing vacuum with a low installed cost and provide years of trouble-free operation. They will continue to evolve with the development of new materials of construction, new nozzle configurations and other innovations that will enhance their benefits.
Croll-Reynolds Company, Inc., 751 Central Avenue, P.O. Box 668, Westfield, NJ 07091. Tel: 908-232-4200; Fax: 908-232-2146.