Why You Should Consider Automation For Packaging-Line Changeover
By Isaac Fletcher, contributing writer, Food Online
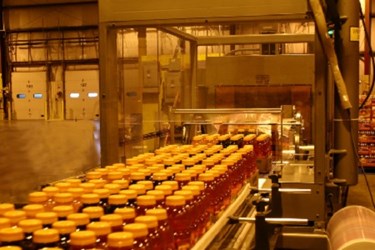
Many manufacturers are discovering that adapting packaging lines to meet a variety of consumer demands has become a necessary part of remaining competitive. By automating line changeover, manufacturers can reduce downtime, improve efficiency, and increase profits.
Packaging line changeovers to adjust for packages of a different size, shape, or material can bring operations to a standstill as system settings are adjusted to accommodate new needs. To make matters worse, bringing a system back to optimal speed too rapidly can result in damaged products, unnecessary waste, and further downtime to make additional adjustments. With recent advancements in sensor and automation technology, manufacturers can optimize line changeovers to reduce downtime and improve productivity.
Decreased Variety Vs. Increased Costs
With a surge in the variety of products demanded by consumers, the need for efficient line changeovers is greater than ever. With conventional changeover procedures, many packagers cannot help but see changeover downtime as an inevitable part of conducting operations. This view leads many to avoid customizing products to fit the demands of regional markets. Alternatively, some manufacturers may opt to dedicate lines to specific SKUs, which take up value floor space and decrease overall production capacity.
With modern changeover technology, manufacturers are no longer forced to choose between decreasing product variety — which detracts from market share — and increasing production costs — which hurts bottom lines. In facilities where line changeovers are a common occurrence, there are a variety of solutions to automate the changeover process, resulting in reduced downtime and higher, more-consistent throughput.
Small Batches With Large Demand
Changeover efficiency has always been a goal for manufacturers, but with the growing demand for on-demand and customized packaging, improving line changeovers has become a major priority. On-demand and customized packaging requires fewer hours and more-varied batches than typical production of a single product, which can run for days at a time.
Accordingly, many manufacturers are discovering that manual line changeovers are no longer good enough. The process of manual changeover is time consuming and opens the door for errors, lost time, and wasted materials. Of course, the issue is worsened as the amount of necessary changeovers during a period of time increases. These factors, coupled with the high cost of labor, can put manufacturers at a significant disadvantage in a highly-competitive industry.
Technologies In Changeover Automation
New technology has allowed for automated changeover systems, which eliminates many of the aforementioned problems by replacing manual parts — hand wheels, mechanical stops, etc... — with intelligent sensors, drives, and programmable logic controllers. In many cases, manual systems can be easily adapted to become automated, regardless of the system’s complexity or type of machines it contains. By preserving and enhancing existing system equipment, manufacturers can receive continued benefit from one of their highest areas of capital investment.
Increased Productivity Via Flexibility
Generally, an automated system can afford manufacturers the specific flexibility to fit their unique needs. For example, systems can be tuned to adjust for a particular product input, a seasonal change point, or replace a motor drive. The changeover system can be leveraged to apply the valuable knowledge and experience manufacturers possess when it comes to their product, and allow the machines to execute the mundane and tedious tasks.
Automated changeover systems also provide benefits to workforce efficiency, as operators can focus on other tasks and maintenance crews are not distracted from other duties to fix problems that arise from errors in manual changeovers. Safety and hygiene are two other areas that are significantly improved by automation. Lower rates of human contact with equipment can result in reduced rates of injury and product contamination.